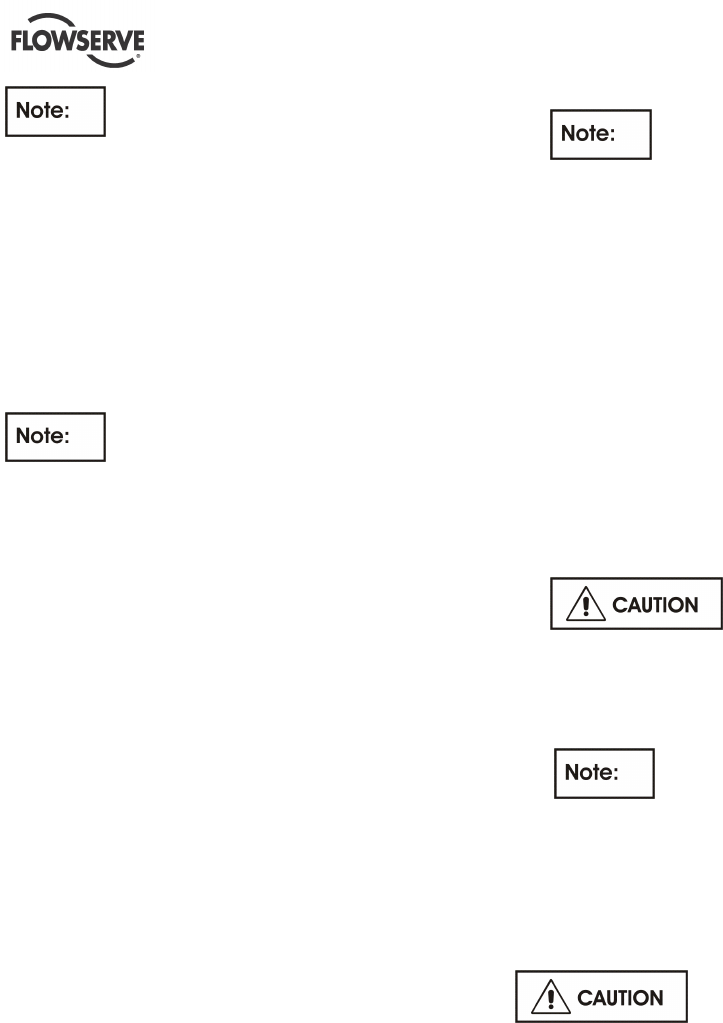
WXB USER INSTRUCTIONS ENGLISH - 07/14
Page 33 of 51
Gaps apply approximately for wear rings
in assembled condition.
6.9 Assembly
To assemble the pump consult the sectional
drawings.
Ensure threads, gasket and O-ring mating faces are
clean. Apply thread sealant to non-face sealing pipe
thread fittings.
6.9.1 Assembly of hydraulic cartridge
Be sure that the casing wear rings
[1500.1,1500.2] are pressed in the stage casings
[1160.1] respectively in the suction casing [1130], the
impeller wear ring[2300.1, 2300.2] are pressed on the
impellers [2200.1, 2200.2]. The rings should be fitted by
tack welding or if necessary by grub screws. The same
applies to the interstage bush [1610] in the diffusers
[1410.1] and the packing seating ring [4133] in the
stuffing box housing [4110].
1) Assembling of the pump is easier in vertical
position (horizontal position is possible too). Use
the reverse procedure as described in the
chapter 6.7.5 Dismantling of hydraulic section.
2) Put the suction casing [1130] with the line bearing
side down on a suitable support. Now insert the
shaft in the suction casing screw it on a vertically
positioned screw.
3) Put the key [6700.1] for the first stage in the shaft
groove. Slide the first impeller [2200.2] from
upwards carefully on the shaft till it touches the
shoulder on the shaft. Adjust the shaft inclusive the
impeller in reference to the suction casing by
turning the shaft in the device. The right position is
reached when the casing wear ring in the suction
casing is even with the impeller wear ring of the
first stage. This visual check is sufficient because
the exact position of the shaft will be committed by
assembling the thrust bearing.
4) Now put from upwards the stage casing [1160.1]
together with the tightly sitting diffuser [1410.1] , o-
ring [4610.7], interstage bush [1610] and casing
wear ring [1500.1] over the shaft [2100] and the
impeller [2200.1] down to the suction casing [1130].
5) Slight the interstage sleeve [2410] on the shaft,
taking care that it catches the key [6700.1]. When it
isn’t the case all parts on the shaft would be
displaced to the thrust bearing and after the pump
is complete assembled it would not turn.
6) Be sure to follow the reverse sequence of all parts
according to the one of dismantling. Watch the
numbers designated at dismantling.
7) After mounting the diffuser of the last stage
[1410.2], put on the cup springs [4263] and finally
the discharge casing [1140] together with the bush
[1600].
The bush [1600] is screwed with
socket head cap screws [6579.3] to the discharge
casing [1140]. Don´t forget the o-ring [4610.6]
8) Slight the balance drum [6230] on the shaft, so that
the groove on it catches the key [6700.1]. Put the
retaining ring [2530] in the groove on the shaft,
slight the ring [1240] over it and fix it with the
socket head cap screws [6579.2].
9) Now assembly the line bearing and thrust bearing
side including mechanical seals. Refer to chapter
6.9.2, 6.9.3 and 6.9.4.
10) Put on the o-rings [4610.9] to the discharge casing
[1140], the o-rings [4610.10] to the last stage
casing [1160.2] and the o-rings [4610.11] to the
suction casing [1130].
11) Now the hydraulic cartridge is fully assembled and
can be put into the casing [1100]. Use the joining
piece for barrel [3121.1] with the help of the stud
[6572.4] for final pulling off the hydraulic cartridge.
By putting the hydraulic
cartridge into the barrel take care of the o-rings
[4610.9, 4610.10, 4610.11].
12) Now tight crosswise the hex nuts [6581.1] of the
studs [6572.1]. For final torque refer to section
6.5, Fastener torques.
The pump can also be assembled by
putting the hydraulic parts piece per piece into
the barrel.
6.9.2 Assembly of shaft seal
Slide on the mechanical seal cartridge to the shaft
[2100] and fix it to the stuffing box housing [4110]
using hex nuts [6581.4] and studs [6572.2].
If the mechanical seal is
equipped with a pumping device, pay attention to the
correct sense of rotation of the same (line bearing
side is different from thrust bearing side).
1) For assembly of shaft seal use the reverse
procedure as described in section 6.7.4
„Dismantling of mechanical seal“. Afterwards follow
the instructions in section 6.9.3 „Assembly of the
thrust bearing side“ or section 6.9.4 „Assembly of
line bearing side“.
2) Replacing the mechanical seal extreme cleanness
is recommended. The sealing faces of the
mechanical seal must be free of scratches or other
damages and have to be cleaned once again
before assembly.
3) Before sliding the rotating parts on the shaft
respectively on the shaft sleeve, the fits must be
sufficiently lubricated with a molykote paste. Take
care that the sealing faces remain clean and no
grease touches them.
4) For those mechanical seals equipped with single
Comments to this Manuals