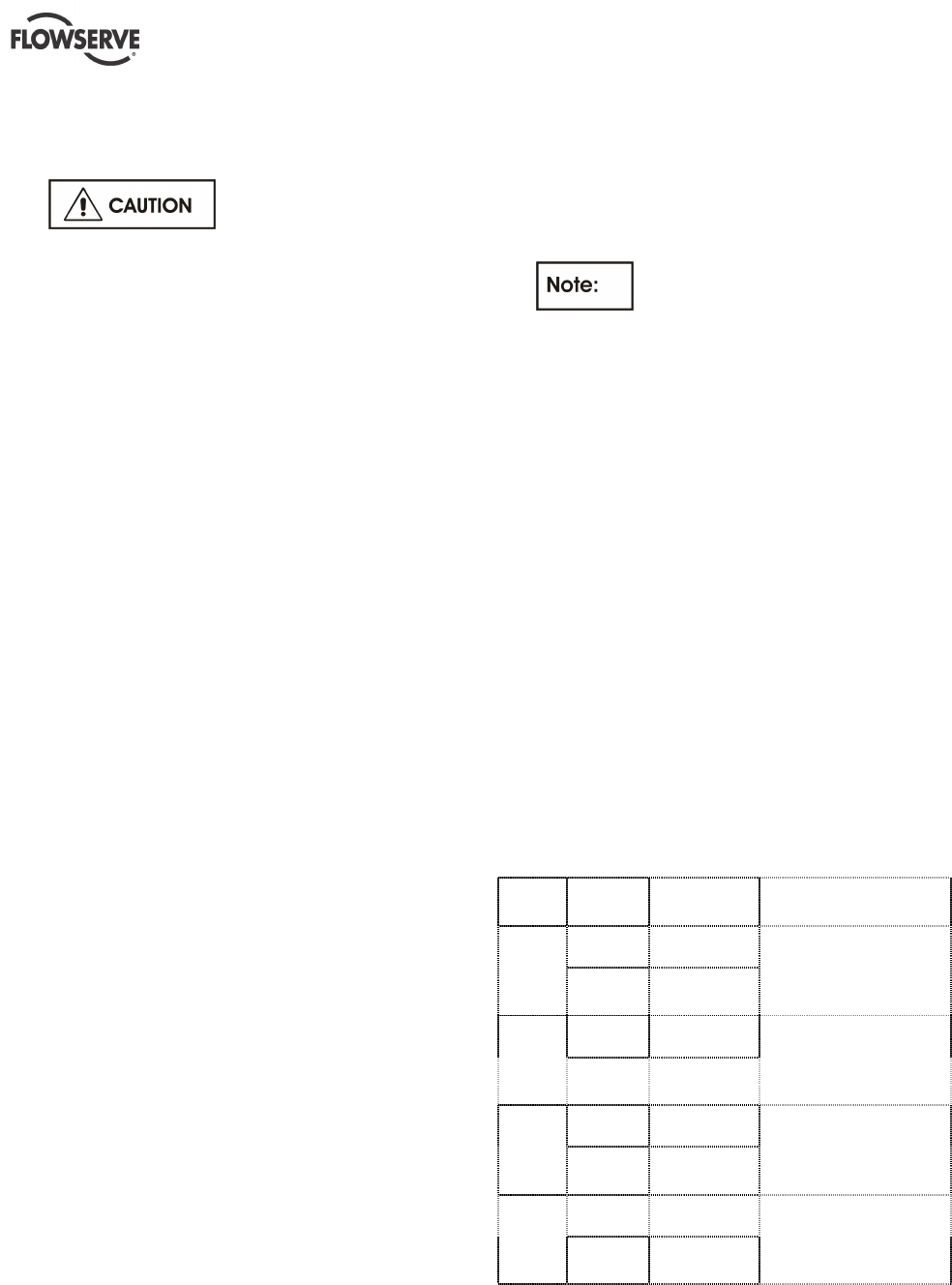
WXB USER INSTRUCTIONS ENGLISH - 07/14
Page 40 of 51
7.6.4 Dismantling of mechanical seal
1) Secure the mechanical seal by putting the mounting
plates into the groove of the shaft sleeve. Loose the
grub screws, and disconnect the seal piping.
Drain the seal system, if
applicable.
2) Loose hex nuts [6581.4] and pull off mechanical seal
cartridge from the shaft. [2100]
7.6.5 Dismantling of hydraulic cartridge
1) Start at the line bearing side first following chapter
6.7.2 and 6.7.4.
2) As next step dismantle the thrust bearing side
following chapter 6.7.3 and 6.7.4.
3) The further dismantling has to be executed from the
thrust bearing side. Remove the o-ring [4610.4] and
draw the stuffing box housing [4110] out of the
discharge casing [1140].
4) Open the hex nuts [6581.1] of the studs [6572.1] and
dismantle the pump stage by stage beginning at
thrust bearing side.
5) First off all loose the socket head cup screws
[6579.2] at the balancing drum [6230]. Then remove
the clamping ring [1240], which is fixing the retaining
ring [2530]. Now pull the balance drum [6230] from
the shaft.
6) Now take the cup spring [4263] and the diffuser last
stage [1410.2]out of the pump.
7) Start to dismantle the pump stage by stage. All parts
of a stage (impeller [2200.1, 2200.2], diffusers
[1410.2, 1410.1], the captive rings [2530.2] and
stage casing [1160.1] have to be numbered to
assure a reassemble in original sequence. The
availability of a crane to secure the heavy parts
would be very helpful, to avoid that they will fall on
the shaft and damage or bend it.
8) Support the stage casing which is next to the
discharge casing. Lift the discharge casing inclusive
the bush [1600], which is fixed on it and also the
diffuser of the last stage [1410.2] which is close in
the casing. When necessary remove the bush from
the discharge casing by loosen the socket head cap
screws [6579.3]. By removing the o-ring [4610.6] out
of the discharge casing with the help of a sharp tool
also the diffuser can be removed.
9) Now remove the captive rings [2530.2] and draw off
the impeller [2200.1] with the impeller wear ring
[2300.1] from the shaft. Then take the key [6700.2]
out of the groove and support the next stage casing
[1160.1] which is closer to the suction casing and lift
the last stage casing inclusive diffuser [1410.1] and
casing wear ring from the pump.
10) As next step remove the interstage sleeve [2410] ,
the impeller [2200.1] with the impeller wear ring
[2300.1] and the captive rings [2530.2] from the
shaft. Now take again one key [6700.1] from the
shaft and support the next stage casing. Remove
the next stage casing still you have reached the
suction casing [1130].
11) Remove the impeller first stage [2200.2] with the
impeller wear ring [2300.2]. Then you can draw the
shaft out off the suction casing. Pull out the suction
casing [1130] from the casing [1100]. In the suction
casing you can find the casing wear ring for the first
stage [1500.2].
Pumps equipped with an inducer
have a separate stage casing in front of 1st
stage impeller.
7.7 Examination of parts
1) Check the casing wear ring and the impeller wear
ring against any wear. The diametrical clearance
between the rings must not exceed twice the
value in new condition.
2) Check all parts against corrosion and erosion.
3) Carefully check the coupling against any wear.
Rotate the angular contact bearing by hand, to
check against abnormal sound. Check the
bearing cages against any wear and the outer
and inner race against running marks. Check the
runout of the shafts. TIR (Total Indicated Runout)
shall not exceed 0.04 mm/m (0.0005 in./ft) of
length. TIR shall not exceed 0.08 mm (0.003 in.)
over total shaft length.
7.7.1 Gap between particular parts
The diametrical gap between casing wear rings
[1500.1, 1500.2] and impeller wear rings [2300.1,
2300.2] in assembled condition is:
Pump
size
Material
Diametrical
gap
diametrical gap between
balance drum [6230] and
bush [1600] mm (in.)
2 WXB
Steel rings
mm (in.)
0,4 (0.016)
0,3
(0.012)
Stainless
rings
mm (in.)
0,5 (0.019)
3 WXB
Steel rings
mm (in.)
0,45 (0.017)
0,4
(0.016)
Stainless
rings
mm (in.)
0,55 (0.022)
4 WXB
Steel rings
mm (in.)
0,45 (0.017)
0,35
(0.014)
Stainless
rings
mm (in.)
0,55 (0.022)
6 WXB
Steel rings
mm (in.)
0,45 (0.017)
0,4
(0.016)
Stainless
rings
mm (in.)
0,55 (0.022)
The diametrical gap between diffuser [1410.1] or
interstage bush [1610] and interstage sleeve [2410] is
0,25 mm (0.010 in.).
Comments to this Manuals