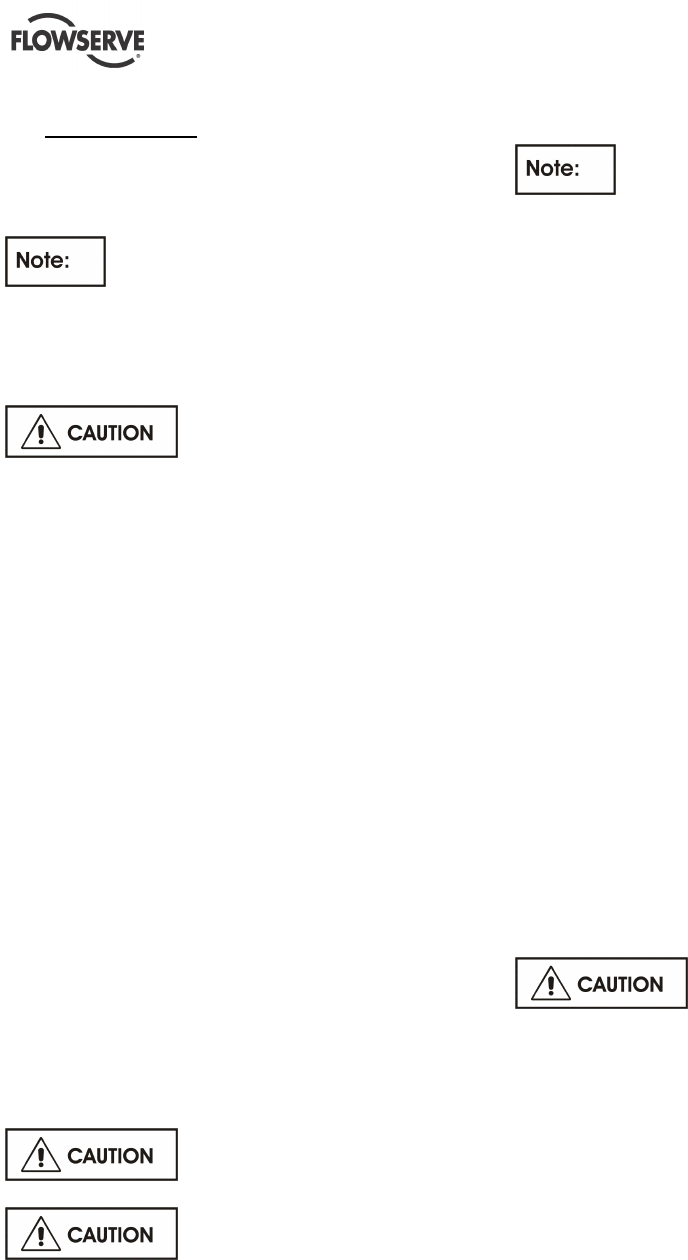
WXB USER INSTRUCTIONS ENGLISH - 07/14
Page 43 of 51
8.0 AUXILIARIES
8.1 Seal and seal systems
8.1.1 Single Mechanical Seal with API–Plan 11+61
Refer to mechanical seal drawing and
auxiliary piping drawing.
The pump is equipped with a single mechanical seal.
The cartridge design allows to change the
mechanical seal without taking it apart.
Try to turn the rotor by hand.If the
rotor cannot be turned, the pump must be
disassembled, refer to section 6.7.1 Dismantling
WXB.
Actions after start up:
Check all connections to the seal gland and the
mechanical seal itself against leakage. It is usual that
at the seal faces a small leakage occurs after start
up, which decreases with the time of operation and
should stop after the seal is run in. Check the
temperature of the seal gland. I slight increase of
temperature may be observed during the run in
period. The mechanical seal is flushed by an API
Plan 11 and the temperature at the seal gland should
be max. 10 °C (18 °F) above the pumped liquid
temperature, unless otherwise specified by
mechanical seal supplier.
In Plan 11, product is routed from the pump
discharge via an orifice to the seal chamber to
provide cooling for the seal and to vent air or vapors
from the seal chamber. Fluid then flows from the seal
cavity back into the process stream.
API Plan 61 has tapped and plugged connections for
the purchaser´s use. Typically this plan is used when
the purchaser is to provide fluid (such as steam, gas, or
water) to an external sealing device.
Refer to the GA - drawing for the
required quench medium, pressure and flow.
Disassembly of the seal cartridge
is only allowed by authorized personal. Contact
Flowserve for any service of the mechanical seal. We
recommend to have a spare cartridge seal on stock
for easy replacement.
8.1.2 Dual Mechanical Seal unpressurized with
API–Plan 23+72+76
Refer to mechanical seal drawing and
auxiliary piping drawing.
The pump is equipped with a dual mechanical seal.
The cartridge design allows to change the
mechanical seal without taking it apart.
The seal cartridge consists of a contacting wet inner
seal and a dry containment seal. A buffer gas is used
to sweep inner seal leakage away from the outer seal
into a collection system and/or provide dilution of the
leakage, so that emissions from the containment seal
are reduced.
The plan 72 system is intended to function as follows:
The barrier gas first flows through an isolation block
valve and check valve provided by the purchaser. It
then enters a system, usually mounted on a plate or
panel, provided by the seal vendor. An inlet block
valve on the panel is followed by a 10 µm (0.0004 in.)
filter coalescer (if specified) to remove any particles
and liquid that might be present. The gas then flows
through a back pressure regulator (if specified) which
is set at least 0.5 bar (7 psi) above atmospheric
pressure. Next comes an orifice to provide flow
regulation followed by a flow indicator to measure
flow. The pressure indicator is used to ensure the
pressure is not above the seal chamber pressure.
The last elements on the panel are a check valve and
block valve. Buffer gas is then routed to the seal
using tubing. A containment seal vent (CSV) and
drain (CSD) are also located on the gland.
The inner mechanical seal is flushed by an
API Plan 23.
Try to turn the rotor by hand.If the
rotor cannot be turned, the pump must be
disassembled, refer to section 6.7.1 Dismantling
WXB.
Actions after start up:
Check all connections to the seal gland and the
mechanical seal itself against leakage. It is usual that
at the seal faces a small leakage occurs after start
up, which decreases with the time of operation and
should stop after the seal is run in. Check the
temperature of the seal gland. I slight increase of
temperature may be observed during the run in
period. The mechanical seal is flushed by an API
Plan 23 and the temperature at the seal gland should
be below the pumped liquid temperature (refer to
mechanical seal drawing for temperature limit).
Plan 23 is the plan of choice for all hot water
services, and it is also disirable in many hydrocarbon
and chemical services where it is necessary to cool
Comments to this Manuals